- Client:
Grupa Azoty Zakłady Chemiczne “Police” S.A
- Object of the task:
“Execution and exchange of heat exchangers 17 / 18E601A and 17 / 18E601B”. Exchangers located in the area of the Nitro Business Unit – Ammonia Synthesis Department at Grupa Azoty Zakłady Chemiczne “Police” SA
- The scope of the works:
The scope of the task included the development of design documentation for the execution and acceptance, execution and delivery of exchangers, exchange of exchangers on the installation, carrying out the necessary tests, collection by the Office of Technical Inspection and commissioning for permanent operation. Designed, made and installed heat exchangers were manufactured based on and subjected to conformity assessment procedure by UDT-CERT against PED 2014/68 / EU including ASME sec.VIII div.2 and PN-EN 13445. After installation in the workplace, a new thermo-mechanical insulation was made cameras.
Number of exchangers: 4 pieces (17 / 18E601A and 17 / 18E601B) horizontal, undetectable, U-pipe heat exchangers.
Weight: 54.4 tons.
Dimensions: 6400×2500 (length / height). Diameter of the jacket: Ø1500; Diameter of the sieve chamber: Ø1930 (Ø2400 with nozzles)
Interesting facts :
Coat, sieve chamber (sieve bottom), cover made of forged materials (as individual elements) in the following grades: ASME SA350 LF2 CL2, ASME SA336 F22 CL3, ASME SA336 / SA336M. U-tubes Ø 19.05×2.77 for a special order in the grade ASME SA-213 Gr. T22.
Thickness of jacket wall 100mm, cover thickness 410mm, thickness of sieve bottom in the place of drilling holes of 305mm U-tubes. In each screen bottom 1938 holes Ø19.3mm were drilled to the U-tube. Before drilling, the inner side of the sieve bottom is padded with INCONEL 600 material (padding thickness after machining 6mm). The tightness of the tubular insert was ensured by rolling the U-tubes in the tube bottom (at the inlet and outlet) and by making a sealing joint from the cover side.
Hydraulic pressure tests (pressure test of the jacket and pressure test of the pipe space) were carried out on the exchangers made with UDT. The pressure of the jacket space was 275 bar while the pressure of the 387 bar pipe test (holding time min 30 min).
The cover of each exchanger is mounted using 20 pins M140x4 (mass set of stud + nut + washer = 125 kg). The assembly took place with the use of dedicated hydraulic tensioners powered by a 1500 bar hydraulic unit made to order ZRE Katowice S.A. Max. the pulling force during assembly of screw connections was about 2200 kN
The exchangers have been nitrogen-rich during transport and storage to avoid internal corrosion.
Oversize transport carried out by Globtrans Katowice.
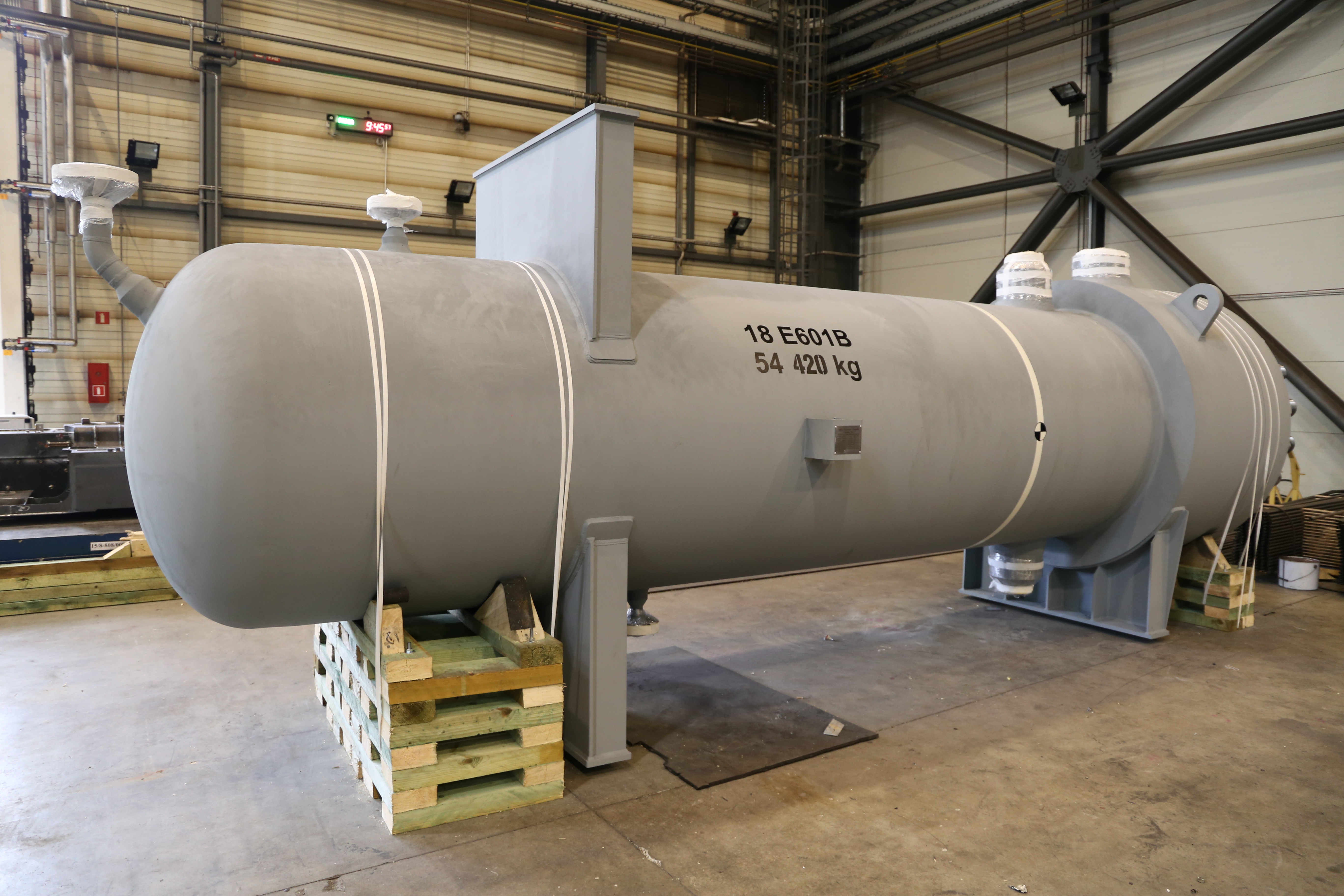
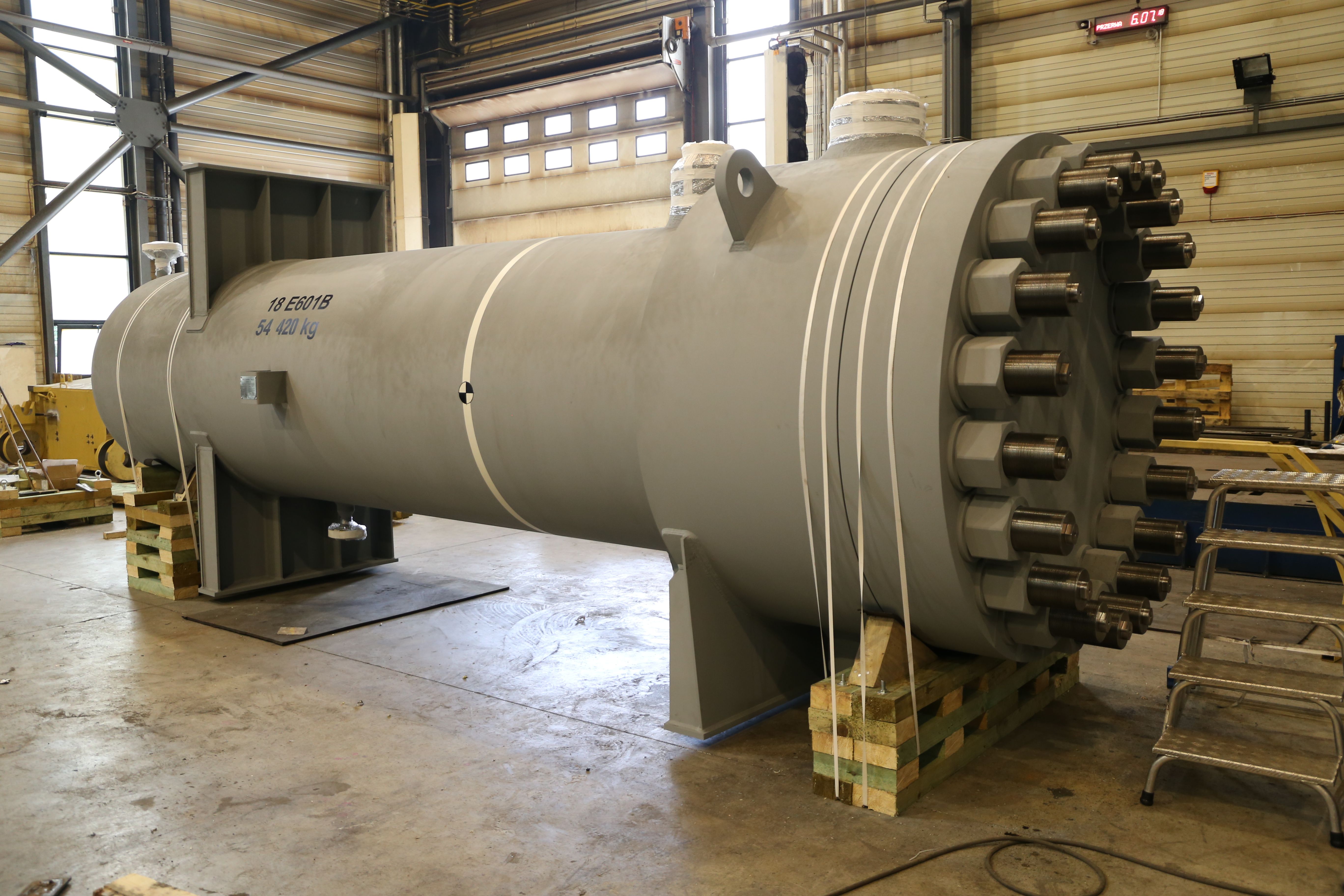
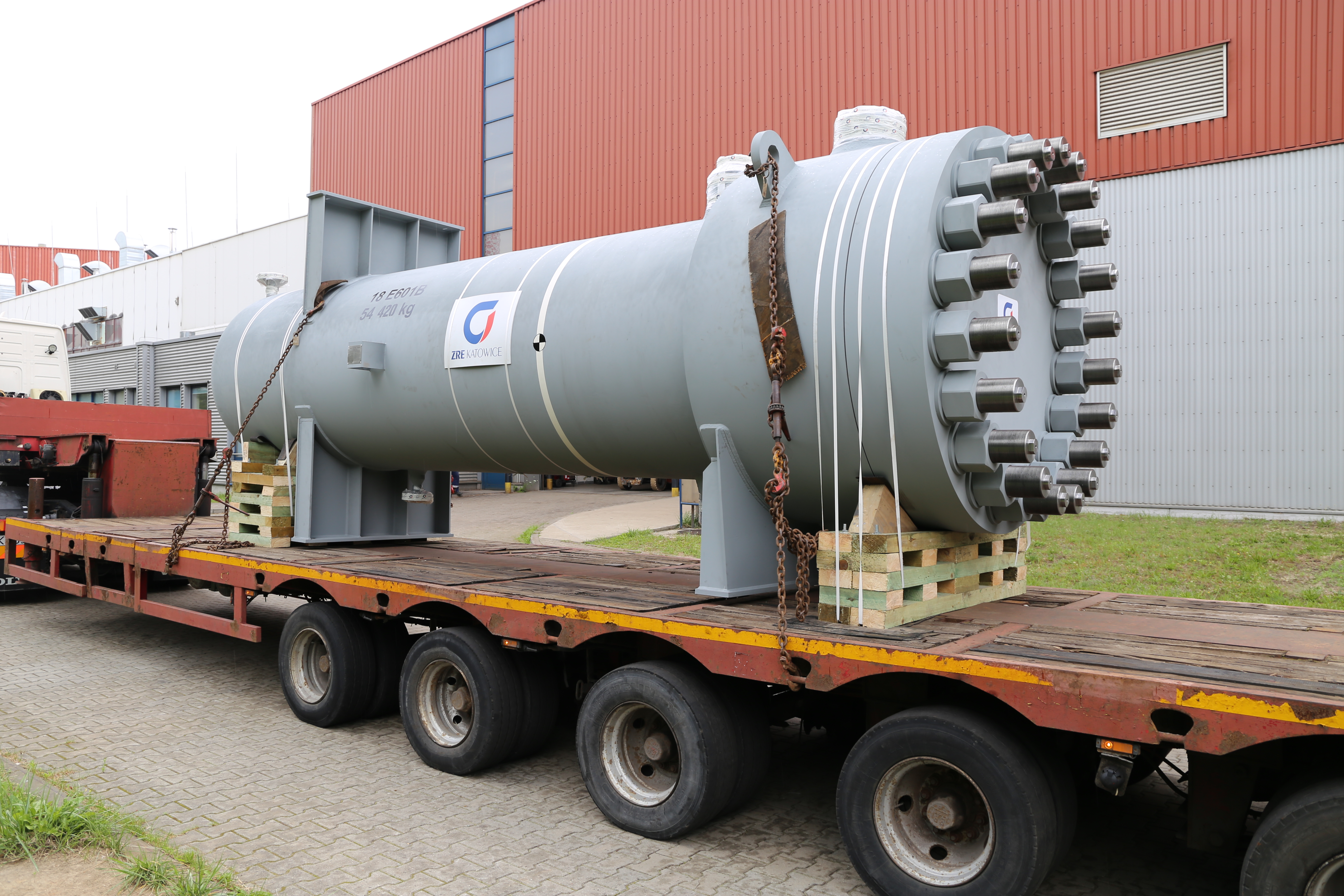
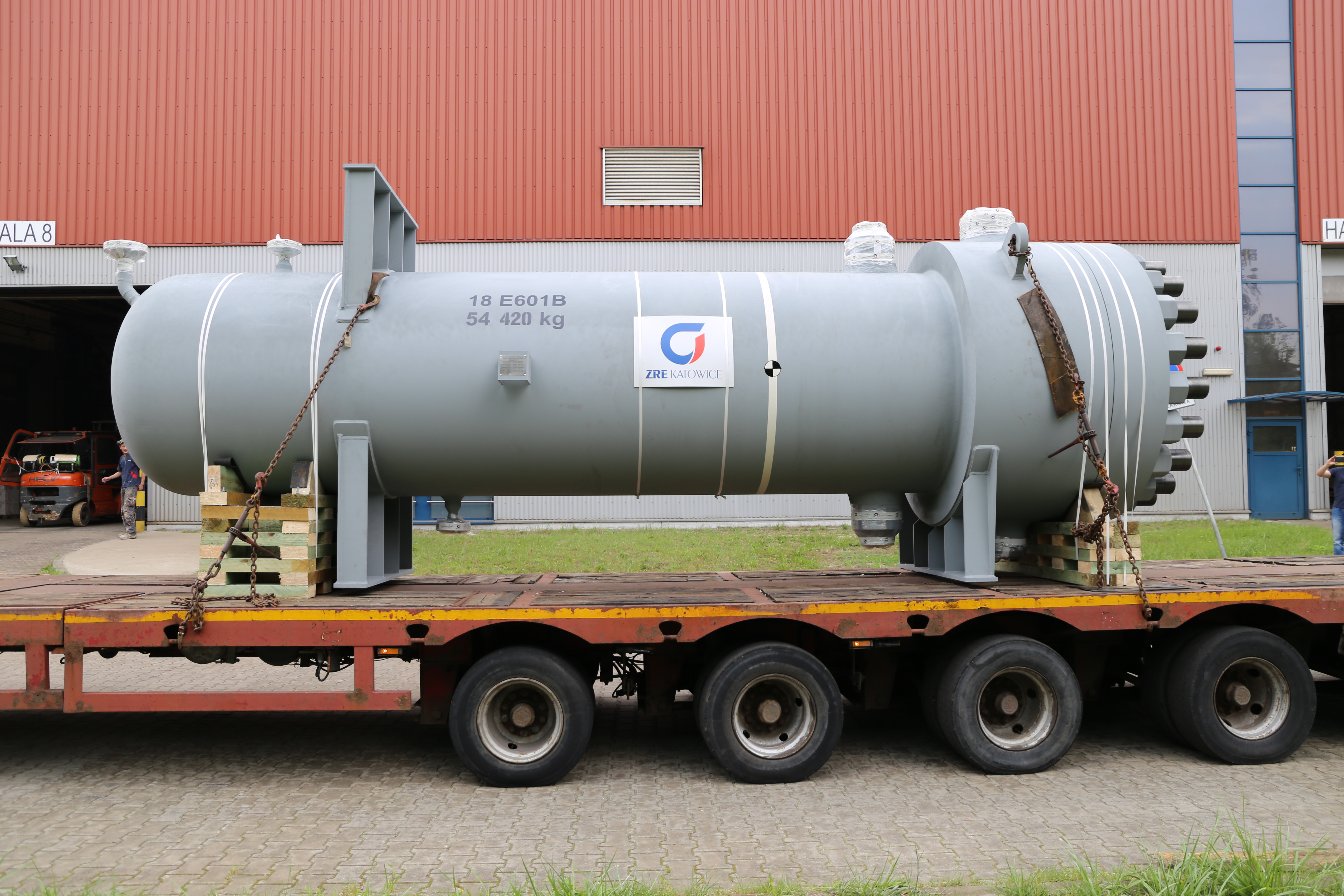
